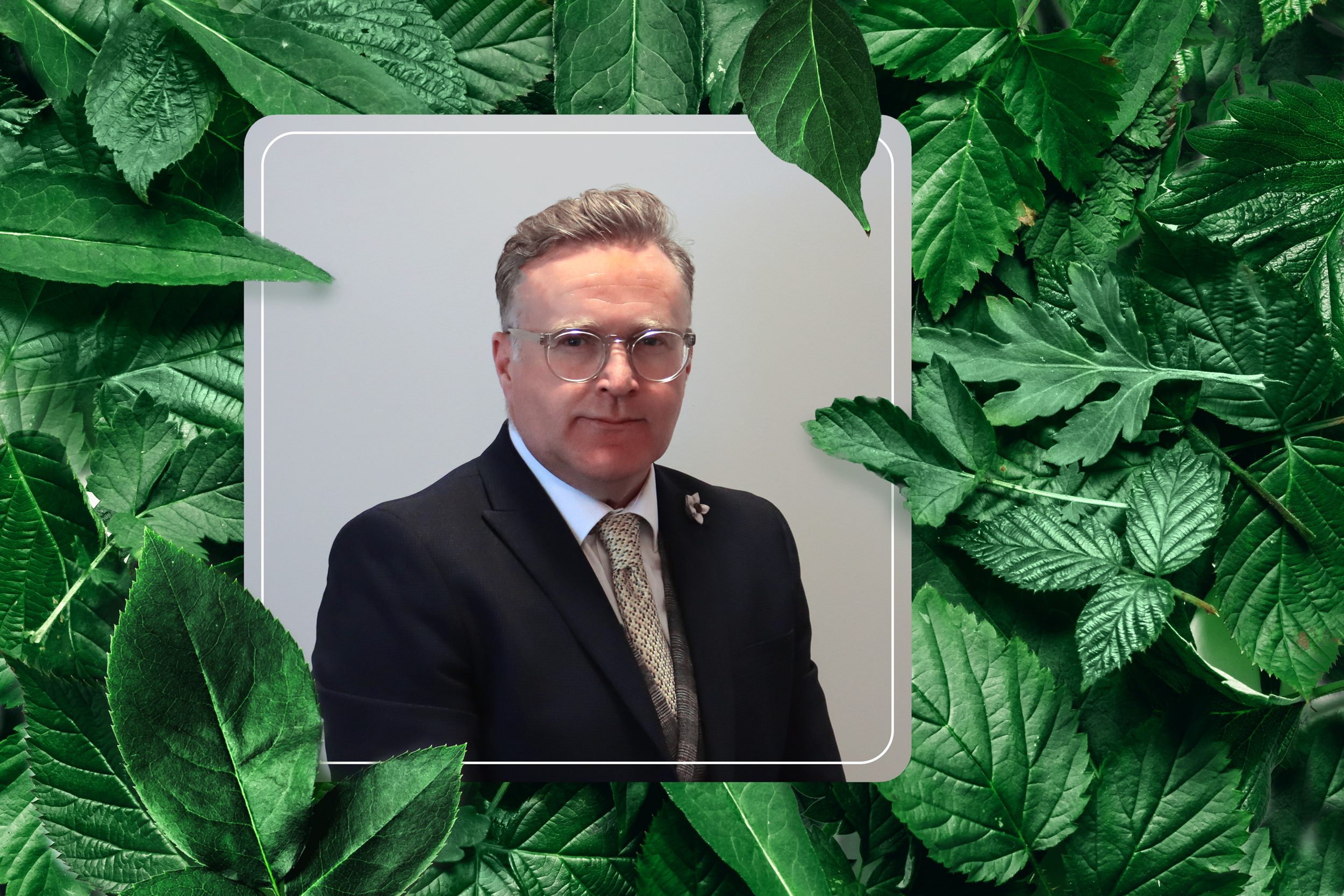
-
- Latest news
- Locations
- Blog
- Client portal
For procurement and operations teams, keeping a warehouse clean brings huge challenges. Concerns like high costs, safety risks, inconsistent quality and staffing headaches are constant obstacles. Insufficient cleaning leads to compliance issues, damaged goods, lower productivity and more. Successfully optimising your warehouse cleaning requires navigating these pitfalls to maximise efficiency and control expenses.
What does it mean to really keep a warehouse clean, and why does it matter? At its core, effective warehouse cleaning accomplishes three crucial goals:
First and foremost, cleanliness is key for safety. Floors free of debris and spills, proper hazard signage, and organisation prevent injuries. A BICS study showed businesses that maintain above-average cleanliness standards have 24% fewer accidents annually. Also, according to Staples Corporation survey, 94% of workers reported feeling more productive in a clean environment, and 77% felt they produced a higher standard of work. A tidy and organised space contributes to better mental states and motivation among employees, ultimately resulting in a more productive and efficient workforce, and providing cost-savings through an enhanced service.
Effective cleaning also enables workflow and inventory processes to operate smoothly. With clutter removed and ample space, products can be moved through the facility efficiently. Workers can also complete tasks faster in an organised environment.
Lastly, cleaning prevents product damage. Removing dust and debris ensures goods avoid contamination or other defects from unclean surfaces and equipment.
If you feel your current cleaning program has room for improvement, here are key factors to evaluate:
Conducting a thorough workflow analysis based on client communication, with flexibility to adjust schedules and team roles to match operational needs, ensures labour can be fully optimised to suit the client, delivering a quality service.
For example, at Samsic, we have developed and implemented a range of LEAN techniques and innovations that help us standardise service quality, eliminate hygiene defects and variability, and provide clean, healthy, attractive, and cost-effective facilities. Our LEAN toolkit, based on the application of our intelligent, science-led solution design principles, comprises 8 consistent elements found throughout all Samsic service models:
Utilising our LEAN toolkit as a foundation for our operations allows us to optimise labour by structuring workloads for specific geographical areas and making technological recommendations to maximise quality. For instance, trialling Co-botic floor cleaners at the Kraft Heinz distribution centre enabled efficient cleaning of a vast site, maximising labour time on-site, allowing our teams to concentrate on more critical activities and deeper-cleans elsewhere.
Collaborative service approaches have been successfully implemented at Coty Bournemouth, where staff have been cross-trained to work within multiple functions. This approach empowers the team, minimises inefficiencies, and fosters a ‘one team’ ethos built on teamwork and empowerment.
Cleaning operatives in warehouses and distribution centres work among active client operations which often utilise heavy-duty machinery and processes, increases the risk of danger for the cleaning teams.
At Samsic, our warehouse and distribution cleaning teams receive a weekly manual detailing their duties, guiding them on what tasks to complete, in what order, instructions, and materials to use. This approach allows management to guide the team to clean certain areas around the client’s schedule, minimising risk and ensuring the team has the space and equipment required to perform to the highest standard. Additionally, this guide enhances accountability and safety monitoring by tracking team members’ locations at any given time.
Selecting proactive and company-culture-aligned candidates for the cleaning team is crucial for workforce development. New recruits need to undergo a comprehensive onboarding process, where they are trained in the processes of their new role and effectively manage the equipment and machinery needed to perform their duties. For example, at Samsic, we offer our British Institute of Cleaning Science (BICSc) accredited training centre, which new recruits utilise to gain the necessary knowledge and skills.
Training resources are invaluable in training new recruits and maintaining quality standards over time. The Samsic Learning Management System (LMS) is a valuable tool to maintain standards and empower staff. It offers a wide range of resources accessible through the cloud, covering everything from ‘back to basics’ training for cleaning operatives to health and safety training and courses spanning office skills, finance skills, personal development, and more.
Toolbox talks are widely utilised for our operational cleaning teams. These talks provide an open platform to discuss challenges faced by the cleaning team, allowing management to work alongside the operational team to maintain high standards, discuss different working processes, and aid ongoing improvement within each client contract.
Ongoing training, especially with new equipment, ensures that standards can be continuously improved over time with the introduction of new technology to the team and the client’s premises as required, optimising efficiency and cleaning standards.
Utilising digital tools to track key metrics ensure the work being completed. Regular audits need to be conducted to ensure standards are being met and challenges are being addressed swiftly.
At Samsic, we employ our ECAT digital auditing tool, which enables contract managers to review cleaning standards within the client site in an accessible manner, shared with the client to maintain transparent communication. ECAT records standards, ensuring projects are monitored, communication is maintained with the client, and results are tracked.
Look for proven expertise specifically cleaning warehouses or manufacturing facilities at your scale. They should understand potential risks and how to mitigate them.
An effective partner will tailor schedules, staffing and procedures to match your workflows and facility layout. They adapt as your operational needs evolve.
Well-trained cleaning operatives that undergo drug screening and background checks are crucial. Look for active training programs and resources. Low team turnover is key.
Safety protocols should be robust. All cleaning operatives should be educated on working around warehouse equipment and inventory safely. Proper equipment and techniques prevent risk.
The partner should actively engage with you to maximise quality and value. Both sides should regularly review data like audits and metrics to identify areas for improvement.
By approaching warehouse cleanliness strategically and partnering with cleaning experts, you gain an asset that contributes directly to operational excellence in safety, compliance and profitability.
At Samsic, we have successfully implemented innovative processes and cutting-edge technologies for our clients, helping them to achieve remarkable results, including:
Improvement in cleaning efficiency
Decrease in staffing costs
Increase in operational efficiency
Optimising cleaning procedures within your warehouse or distribution centre can significantly impact both the operational performance and bottom line of your business.
We have a proven track record, serving clients such as Coty, Boden, Selfridges, and Holland & Barrett with top-tier facilities management services. Our success is attributed to our strong capabilities as a supplier.
A willingness to collaborate and innovate, fostering a partnership between the cleaning provider and the client, enables fluid communication, fast issue resolution, and cultivates a culture of continuous improvement. At Samsic, our longstanding relationship with the Kraft Heinz Company is built on collaboration and innovation, allowing for swift approval and application of new processes and equipment to the contract. Regular audits and discussions on areas of improvement can be quickly implemented, avoiding major contract discrepancies and issues. Through regular communication, the structure and timing of tasks can be efficiently adjusted to suit client operations.
At Coty, where we handle cleaning for three of their UK distribution sites, our successful service led us to become a full facilities management provider for their 22,000 square meter Coty Bournemouth site—a crucial component of the organisation’s UK operations. It’s essential for all clients to receive a tailored service that aligns with their specific needs and contractual requirements. Investing in our people was key to the success we achieved at Coty Bournemouth. We heavily invested in training and boosting team morale, resulting in a versatile, high-standard workforce capable of working independently across a large geographical area, covering multiple facilities management duties if necessary. This investment significantly contributed to our successful services at Coty, resolving previous issues within the cleaning operations.
Emphasising staff training and capabilities can be pivotal for a provider’s success. Opting for a cleaning provider that prioritises training ensures your service benefits from new processes, research, materials, and potentially technology that can support both service quality standards and your business operations.
Head of UK Sales
Business Development Manager, London and South Region
Business Development Manager, North Region