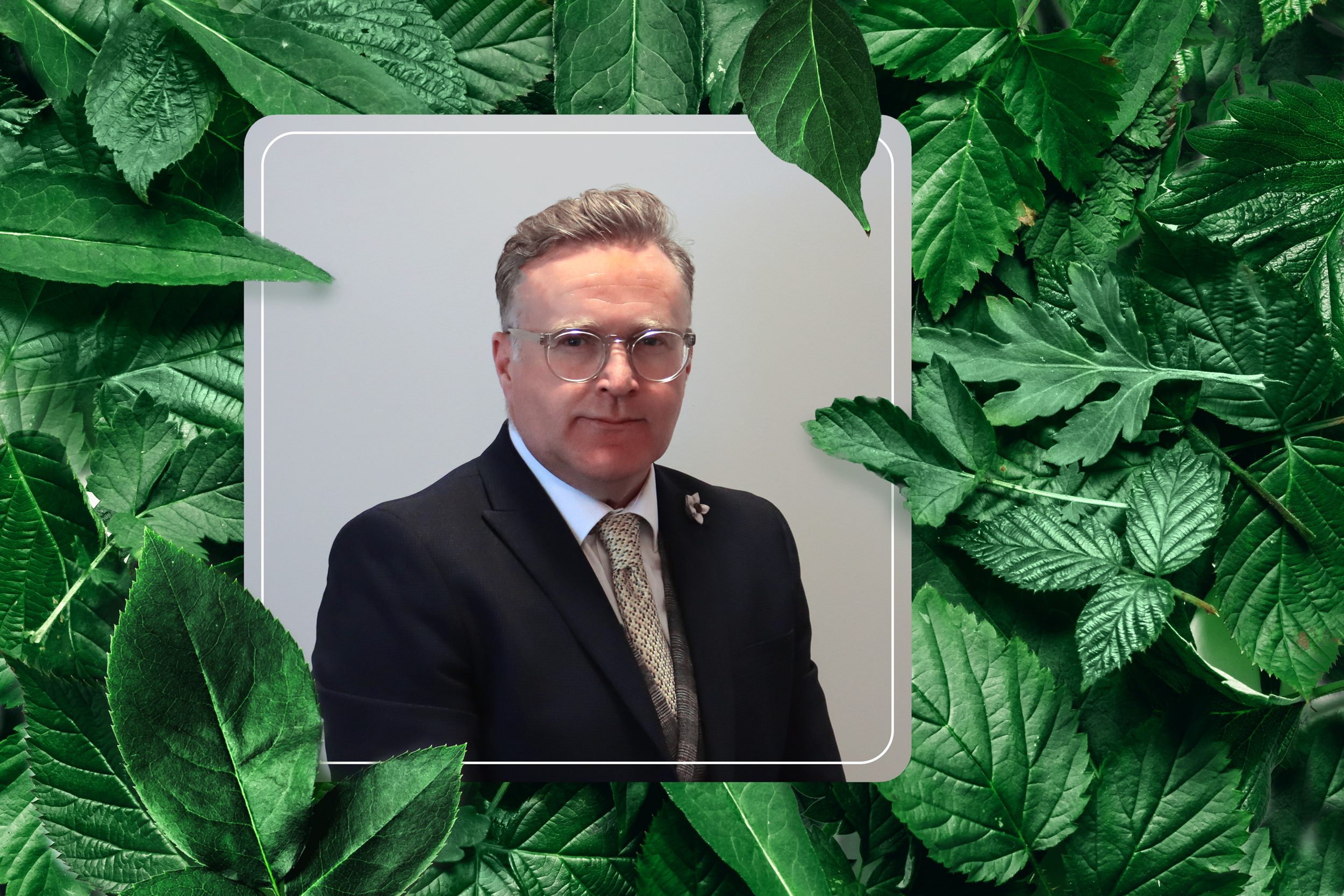
-
- Latest news
- Locations
- Blog
- Client portal
Case Study
The partnership between Samsic and Kraft Heinz, which began in October 2021, has brought about considerable enhancements and innovations, benefiting Kraft Heinz significantly.
The optimisation of shift patterns, especially within the weekend team, being just one example of positive operational amendments. By collaborating with Kraft Heinz to design new flexible shifts that align with changing production needs, Samsic enabled greater productivity and efficiency on-shift. Optimised shifts were made possible by training and upskilling the Hygiene Operatives, expanding their skillsets for greater workforce flexibility.
Operatives now have more knowledge of plant machinery and as such boast enhanced capabilities to benefit the client. The collaboration in amending shifts has unlocked substantial benefits for Kraft Heinz as Samsic now align their cleaning operations to meet changing production needs.
Upskilling the Hygiene Operatives as well as providing operational benefits, also aims to empower operatives, providing them with more skills and areas of growth. Combined with Samsic’s Learning Management System, monetary gifts to recognise exemplary work, and ‘toolbox’ learning meetings, Operatives are encouraged to share their feedback and develop a unified team outlook, boosting morale.
Redesigned weekend shutdown shifts proved to be more efficient, productive, cost-effective and deliver improved results in chemical ATP testing. This crucial 40-hour production shutdown window allows Samsic to thoroughly deep clean all areas, translating to utility savings for Kraft Heinz through enhanced maintenance, i.e. more efficient use of resources, less wastage, better equipment lifespan, and overall reduction in operational costs.
The on-site team’s management structure has been reorganised, offering more support for Hygiene Operatives. This has also enhanced decision-making and made the procedures more efficient at a site that has more than 140 Standard Operating Processes. It’s crucial to manage this site with caution as it can be hazardous if not handled carefully. Positive outcomes observed to date include improved productivity, increased cost savings, and enhanced operational efficiency.
Other benefits to Kraft Heinz from working with Samsic include heightened environmental practices whilst still maintaining and, in many cases improving, service quality and cleanliness. Samsic has reduced janitorial chemicals on site by 36.84%, with views for this to rise to 42.11% by the end of 2023. Water savings of 50% overall have been achieved through a dedicated water saving project.
As a major food production site, Kraft Heinz Kitts Green incorporates heavy machinery and chemicals such as caustic acids as part of their operations, which can pose a major risk to Hygiene Operatives. The site has been in production since 1959, and is open 24/7, with a long-serving workforce operating in shift patterns to cover a 24-hour service requirement.
The Kitts Green site is a bustling hub with a deeply rooted culture that may be challenging to modify. However, introducing fresh values and process structures on-site is essential and presents a unique opportunity to breathe new life into the operations.
The considerable scale of the site creates an exciting challenge for both the cleaning and security services, as they expertly manage the consistent inflow of employees and visitors who are warmly welcomed and checked in.
In the following context, technology plays a critical role. Harnessing technological advancements can not only enhance the experience of visitors and staff but also significantly contribute to reducing incident rates, making it a key component in our ongoing improvement efforts.
As with any food production factory upholding flawless standards of cleanliness and security is critically important, as even a single breach could jeopardise food safety and quality, and accidents on site can have terrible consequences for staff and the reputation of the client alike. To provide an impactful and successful service on-site Samsic must be consistent in the approach to safety, security, and efficiency.
The Kraft Heinz Company has a spirit of ongoing process development and greatly values innovation and efficiency. Samsic, to be able to adhere to and provide a force to ignite these values on-site, employed a Key Account Manager, who has been instrumental in enhancing operations and creating efficiency savings.
On review, cost-savings and enhancements to operations were found in the training of staff, the optimisation of shift patterns, and the optimisation of cleaning materials and technology. The Samsic Innovation Team conducted numerous research projects to find how the factory could be best optimised, with technological advancements such as steam boxes and Co-botics being utilised in extensive trials. The Co-botics trial at Kraft Heinz has concluded with cleanliness standards and efficiency being rated ‘exceptional’, with more time available for the Operatives to perform deep-cleans.
In security, SmartLogic technology has been incorporated to support visitor and staff experience, as the creation of ID cards is now automated. Security staff can here focus on their service approach in welcoming visitors and staff alike on-site, improving experience, and have more capacity to ensure the site is secure through reduced admin tasks.
To ensure that exceptional standards are always being achieved and that processes are constantly being improved and developed, Samsic utilises the ECAT auditing system to manage standards and discusses results with Kraft Heinz senior management on a weekly basis, ensuring projects are being monitored, communicated with the client, and results are tracked.